Chemigation And Fertigation
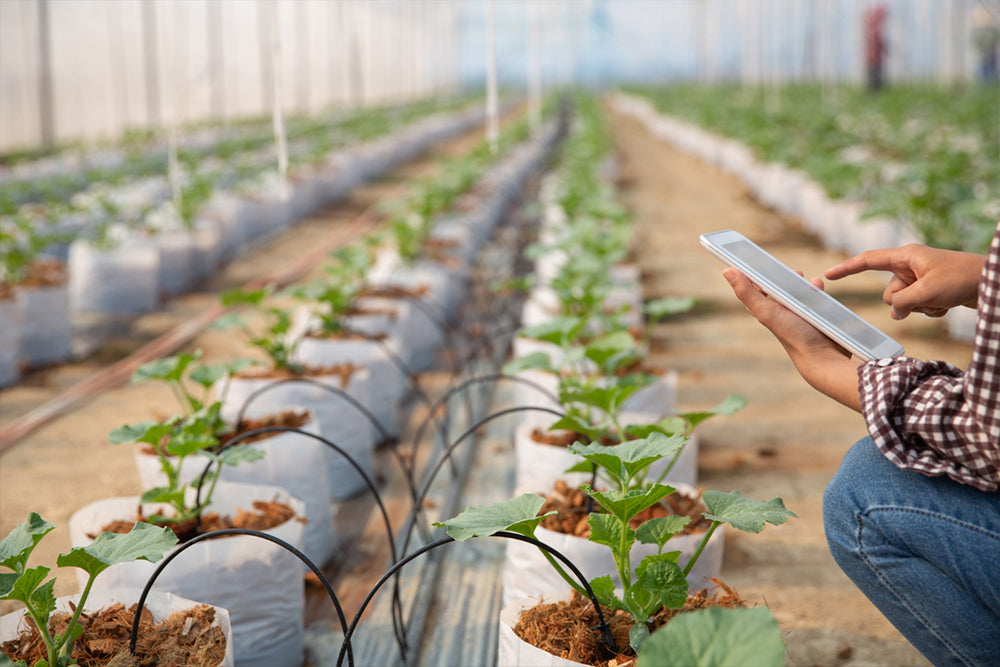
Farmers are increasingly under pressure to save costs and avoid excessive fertiliser and chemical use. Fertigation and applications deliver the accuracy and uniformity required.
For agricultural food production and plant production, the demand for more accurately measured inputs for both fertilisers and chemicals along with water usage has become the norm. The increased cost of all inputs in growing food will only continue to increase as the world’s existing water and farmland resources will need to produce more with less.
The demand for safe food supply places increased demands on the growing and harvesting of food. The use of proper amounts of fertilisers in the growing of those crops and the handling of the harvest as well requires accurate applications of chemicals to ensure that food is not contaminated with any harmful substances.
This is also true for greenhouse and hydroponic farming systems. Something that we all now expect to find on our grocery shelves is fresh fruits and vegetables. The application of the fertilisers and chemicals to keep these growing systems free of any pests or harmful agents is even more critical than with outdoor field crops.Chemical and fertiliser dosing systems are commonplace for both growing and disinfection systems.
What is Fertigation/Chemigation? Fertigation is the application of fertiliser and or soil amendments with your irrigation system water. A fertiliser is a substance that contains one or more plant nutrients to promote plant growth. This can also include gypsum and lime
Chemigation is is the application of pesticides or system maintenance products through an irrigation system. These can include-herbicides, insecticides, fungicides, fumigants, plant growth regulators, rodenticides, disinfectants, sanitisers, buffering agents, desiccants, defoliants, sprout inhibitors and spray adjuvant.
Â
Advantages of Fertigation/Chemigation:
•Uniform application – delivered with irrigation
•The right amount applied to the crop
•Additinal field equipment not necessary, reducing costs and maintenance
•Reduced timelines through applying fertiliser with irrigation
•Reduced compaction
•Reduced risk, as the operator has little or no contact with chemicals or fertilisers
•Reduced overfeeding and underfeeding of the crop
•Avoid the extra equipment andresources for dry applications
Plant production or container nurseries for crops that are transplanted into our fields or gardens need to be clean of any plant or soil-borne pests that may spread and harm existing farmlands or gardens. The use of chemicals and fertilisers ensure growth and that pests are not spread, as well as protecting the environment. Again, the accuracy of fertiliser application into the irrigation system in addition to chemicals to keep the plants free of pests is critical.
The trends today are for increasing environmental regulation and legislation. The monitoring of our groundwater and surface water will see additional regulations due to the risks of the leaching of chemicals and nitrates into our existing water sources. We will need to apply only those fertilisers and chemicals that the plant requires with as little waste as possible. Water runoff from irrigated farmlands will be monitored to a greater extent than today, with increasing local, state and
federal regulations.
In future, demands will increase for application accuracy, for tracking of where food comes from and what was applied to it before it ended on the grocery shelf. The application of fertilisers and chemicals will need to be measured and tracked. The tracking of the data for what was applied to the crop will be collected and monitored and shared with consumers, and with local, state and federal agencies. You can’t manage what you can’t measure and to measure accurately you require state of the art dosing equipment.
With more mechanised irrigation and the ability to apply fertilisers and chemicals through those systems, we will see increased yields. Growers need to stay competitive, have new systems in place, and reduce labor costs. This means applying only those fertilisers and chemicals necessary for maximum crop production, and for keeping our environment safe. This can only be done with precision application equipment.
Accuracy and uniformity offer many advantages
As commercial liquid fertilisers are concentrated and expensive, it is vitally important that the fertigation method used is uniform and precise. If this is not achieved, then the crops can be damaged, or growth across the field becomes irregular.
The increase in the use of pressurised irrigation systems such as drip and sprinklers, mechanised irrigation systems such as center pivots, and other irrigation systems has also seen the growth of fertigation and chemigation. The irrigation systems reduce the time and labor that it once took for the application of fertilisers and chemicals.
The fertigation and chemigation system should also reduce water runoff and reduce environmental issues. As irrigation systems and components have become more efficient and the uniformity of these systems has been improved, so has the efficiency and uniformity of the application of the fertilisers and chemicals.
There are many advantages with fertigation or chemigation applications. If the uniformity of the irrigation system is high, the uniformity of the chemical application will also be high. Uniformity may change due to nozzle wear, operating pressures, valves or other irrigation system components; however it is a straightforward matter to check up on the uniformity of the irrigation system and tune up the system prior to any
nutrient or chemical addition.
The economic advantages are many. Only the required amount of nutrients and chemicals is applied to the field being irrigated, saving costs and reducing waste. Costs can be lowered further by using concentrated solutions. Furthermore, the expense of additional field application equipment is not necessary, and the additional cost of upkeep and maintenance of that equipment is reduced. In all, the application is less labor intensive, and this also makes it easier to meet safety requirements. Application can be automated through the use of integrated dosing systems.
As fertilisers can be applied through an irrigation system, the need to wait for a field to dry after irrigating to allow driven equipment to enter the field is eliminated. Nutrients and chemicals can be applied during the irrigation. Scheduling is much more exact, simplifying timelines.With the irrigation system applying the nutrients or chemicals, additional tractors or spray equipment are not driving through the field, reducing compaction. Hazards to the operator are also
reduced, because chemicals and fertilisers are injected into the water stream with little or no contact with operator. Operators are not in the middle of the irrigated area with chemical or fertiliser application equipment. Solutions can be dosed directly from bulk storage containers without the need for mixing or other handling.
Let the irrigation system
do the work
Choosing a fertigation system means letting the irrigation do the work, and there is no need for costly chemical application equipment that also requires maintenance. Overfeeding and underfeeding of the crop is also reduced, because the uniform application of chemicals and fertilisers is easily controlled for the prescribed quantity over the given area.
Furthermore, dry fertilisers applied by mechanical means require additional equipment such as tractors and fertiliser drills or spreaders. Once applied, they must be irrigated uniformly so that they dissolve at a uniform rate. To achieve a uniform application or reasonably uniform application means either waiting for rain or usinga pressurised irrigation system. If a pressurised irrigation system is used, why not just apply the material through that equipment? The farmer then knows that the correct quantity of material was applied while also irrigating the crop. The overall amount of chemicals applied can be reduced when compared to the dry application. Fertilisers can also be applied several times during the growing season, when required by the plants during the irrigation process.
With the installation of more and more pressurised irrigation systems such as center pivots, drip irrigation systems in permanent crops and tape irrigation systems in row crops, there is an ever increasing ability for applying fertilisers and other chemicals through the irrigation systems. Also, as fertilisers have become more expensive, the requirement is to apply only
Dosing into a center pivot is one example of types of a high-flow fertigation application requiring precision and uniformity.
Drip/micro spray fertigation applications use smaller pumps with low flow with the same requirements for precision and uniformity
what is required with accurate timing and in precise quantities, so that fertilisers remain within the root zone of the crop being fertilised. This reduces the quantity of material and the possibility of leaching of the chemicals past the root zone and being lost. This practice will and has reduced nitrates from entering
our water sources.
Precision application of liquid fertiliser
Fertilisers come in many forms and farmers who have been mixing granular fertilisers into water are now beginning to realise that this may not be the most economical and often can be inaccurate. Pressurised irrigation systems require water soluble fertilisers and many of the dry formulations may contain ingredients that are not totally soluble.
Commercially available liquid fertilisers and effective, accurate dosing devices are becoming the norm. The results are improved crop yields and the use of fewer inputs that also generate greater profits.
Liquid fertilisers have a consistent concentration in content and provide a greater flexibility for fertigation methods, such as foliar spray, soil injection, drip or micro spray. They also reduce the need to handle heavy bags and dust exposure when applying dry materials. Liquid fertilisers eliminate blockages of hoses and tubes and allow rapid uptake.
Precision application is more important now and will continue to be refined. The cost of fertilisers and chemicals will only increase and the precision of application will only need to be improved. The goal must be to apply only what the plants can utilise without any leaching or run off. Chemigation practices must be such that those chemicals applied are only applied to the plant or soil surfaces to which they are intended. The reduction of overspray and wind drift must be accounted for
and eliminated.
Digital dosing pumps bestfor uniformity and accuracy
Of the many pump types that can be used for fertigation applications, motor driven dosing pumps – and even better yet digital dosing pumps – provide extremely high
precision. Digital dosing pumps allow fertilisers to enter the irrigation water pipe line uniformly and well mixed.These pumps also provide flexibility in control through simple manual start/stop or proportional control from a water flow meter.
Commonly available fertigation pump types
The following table provides a comparison between the advantages and disadvantages of the most commonly available fertigation pump types.
Type | Advantages | Disadvantages |
Electric VFD Motor Crank Driven |
|
|
Hydraulic Driven |
|
|
Electric Solenoid Driven |
|
|
Electric Motor Cam Driven |
|
|
Pressure Differential Venturi Driven |
|
|
Electric Motor/Engine and gear box Piston Driven |
|
|
Electric Motor Peristaltic Pump Driven |
|
|
Engine Driven Roller Pump |
|
|